The Basic Structure of FPC

The basic structure of a single-sided FPC is as follows: In traditional FPCs, a copper foil conductor is fixed onto a substrate film, such as polyimide, which is bonded with an adhesive such as epoxy resin. The circuit is then covered with a protective film through etching. This structure has high mechanical reliability due to the use of adhesive materials such as epoxy resin, and is still one of the standard structures commonly used today. However, the heat resistance of the adhesive, such as epoxy or acrylic resin, is lower than that of the polyimide resin substrate film, which becomes the bottleneck that determines the maximum operating temperature of the entire FPC.
In this case, it is necessary to eliminate FPC structures with low heat-resistant adhesives. This structure not only reduces the thickness of the entire FPC to a minimum, greatly improving mechanical properties such as bendability, but also facilitates the formation of fine circuits or multi-layer circuits. A non-adhesive, copper-clad laminate composed only of polyimide layers and conductor layers has been put into practical use, expanding the range of materials available for various applications.
FPCs also have double-sided through-hole or multi-layer structures. The basic structure of a double-sided circuit FPC is similar to that of a hard PCB, with interlayer bonding using adhesive. However, many high-performance FPCs have recently excluded adhesives and used only polyimide resin to form the copper-clad laminate. The layer construction of multi-layer FPCs is much more complex than that of printed PCBs, and they are called multilayer rigid-flex or multilayer flex. As the number of layers increases, flexibility decreases. To increase the freedom of mechanical activity, it is necessary to reduce the number of layers in the bending portion or exclude interlayer bonding. To manufacture multilayer rigid-flex boards, many heating processes are required, so the materials used must have high heat resistance. The use of non-adhesive copper-clad laminates is increasing now.
In this case, it is necessary to eliminate FPC structures with low heat-resistant adhesives. This structure not only reduces the thickness of the entire FPC to a minimum, greatly improving mechanical properties such as bendability, but also facilitates the formation of fine circuits or multi-layer circuits. A non-adhesive, copper-clad laminate composed only of polyimide layers and conductor layers has been put into practical use, expanding the range of materials available for various applications.
FPCs also have double-sided through-hole or multi-layer structures. The basic structure of a double-sided circuit FPC is similar to that of a hard PCB, with interlayer bonding using adhesive. However, many high-performance FPCs have recently excluded adhesives and used only polyimide resin to form the copper-clad laminate. The layer construction of multi-layer FPCs is much more complex than that of printed PCBs, and they are called multilayer rigid-flex or multilayer flex. As the number of layers increases, flexibility decreases. To increase the freedom of mechanical activity, it is necessary to reduce the number of layers in the bending portion or exclude interlayer bonding. To manufacture multilayer rigid-flex boards, many heating processes are required, so the materials used must have high heat resistance. The use of non-adhesive copper-clad laminates is increasing now.
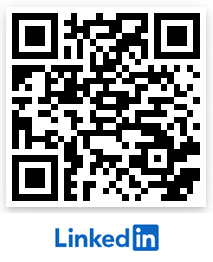
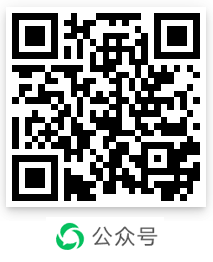